[FAQ] Frequently Asked Questions
Save Time and discover our FAQs – You will find the Answers to your Food Inspection Questions and Food Control Needs in one Place.
Home » FAQ
Biometic - A reliable partner
With BIOMETiC, you are on the Safe Side
From food production to processing: At BIOMETiC, we make your products safer, of high quality, and, just as important,cost-effective.
Our mission is to help food companies like yours, who give their best to provide daily safe and high-quality food to people. That’s why we have collected the most frequent questions and answers to some of your food inspection curiosity and needs. Find below the solution to your questions quickly and easily.
And if you can’t find the answer you were looking for, don’t worry. We know that every company, especially in the food industry, has different needs.
That’s why we offer you the possibility of sending us a free request for a totally free and not binding online demo, where you will quickly get more details about our 3D X-ray inspection solutions, and discover what incredible information our technologies can offer you.
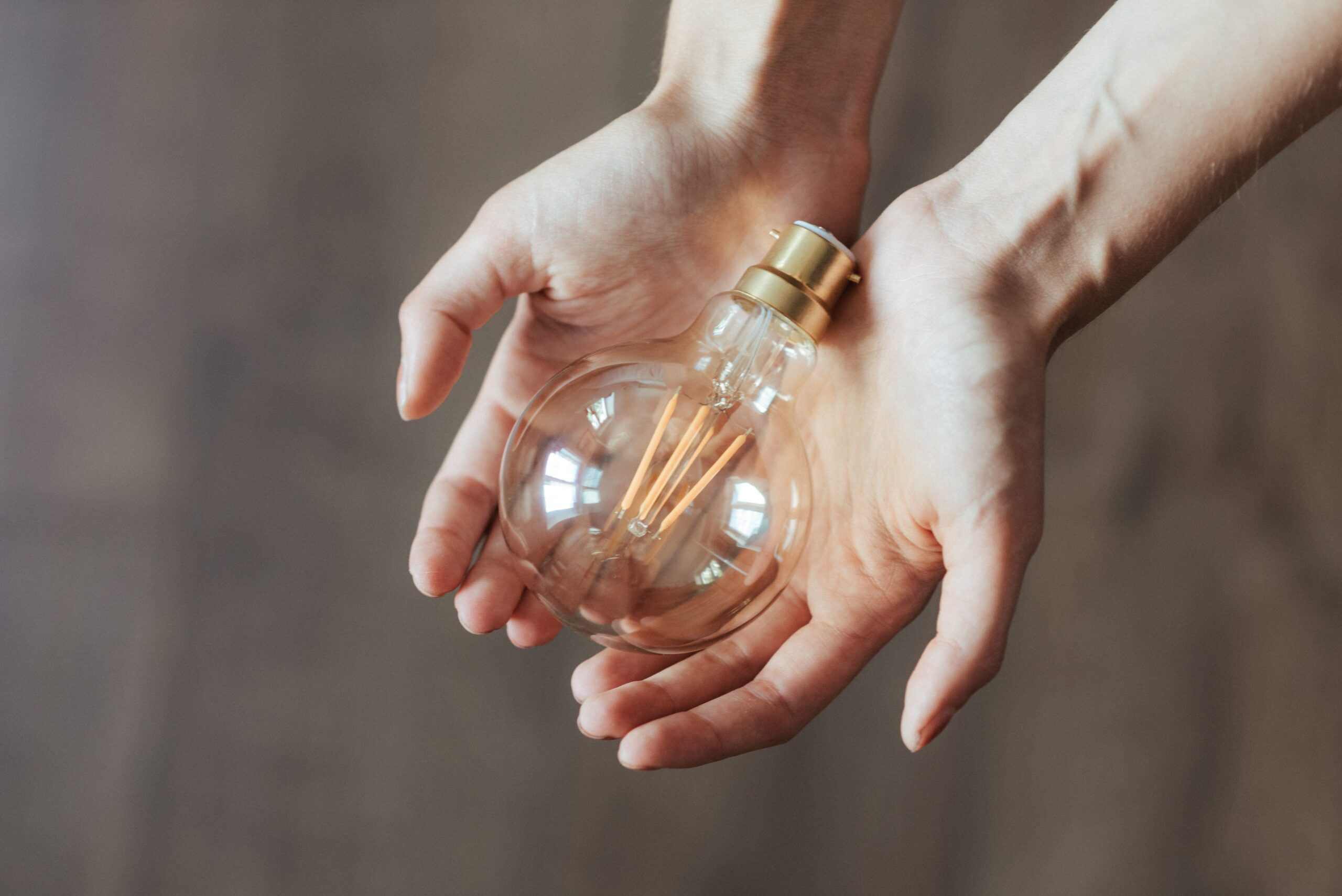
Inspection Solutions for Fruit and Vegetable Cooperatives
We have the answers to your questions about 3D and X-ray food inspection of fruit and vegetables.
Inspection Solutions for the Food Industry
Find the solution to your questions about BIOMETiC’s 3D X-ray inspection systems for processed food products.
BIOMETiC Services and Inspection Solution
Find out more about the services and 3D X-ray solutions we at BIOMETiC offer our customers.
[FAQ] Frequently Asked Questions on BIOMETiC
It depends on the type of BIOMETiC solution application and the product your company processes. But in general, spacing foods products from each other is not necessary.
For example, with the 3D X-ray inspection system Mito, different containers can be scanned simultaneously, even if they are side-by-side and paired.
With Q Eye XP, an X-ray device for the end-of-line inspection of boxed fruits and vegetables and packaged food products, you can simultaneously scan multiple products within a box or package.
Also, with the smart optical sorter Q Eye Smart, you can scan multiple lines of fruits or vegetables side by side at the same time.
The ejection system, as well as the configuration of the chosen BIOMETiC solution, are evaluated and chosen by BIOMETiC together with the customer based on the application, the food product, and the production line layout of the company.
For the ejection systems, you can think, for example, to install mechanical or compressed air ejectors.
Contact us now and find out how easy it can be to integrate a BIOMETiC solution within your production line.
Sure. Data produced by BIOMETiC solutions can also be retrieved and exported at a later date.
Contact us now to get more details on the many benefits a BIOMETiC solution can offer you and your company.
With its accurate system based on multi-sensory approach and 3D reconstruction, Q Eye Smart not only accurately sorts fruits and vegetables based on size, weight, and color, but also on external quality.
Q Eye Smart locates and measures in real-time, for example, the number and position of cuts on the stem cavity of apples.
But it can also determine the “acceptable” percentage of external defects set by the customer.
Q Eye Smart uses these values as ejection criteria for products that do not meet individual quality standards.
Of course, the inspection requirements are adjusted according to the product and company’s needs.
This need is growing rapidly, given the benefits of improved traceability processes. With its complete traceability system, from the goods delivered to the final product, F-Trace guarantees full traceability of your products, even those in stock.
It can be integrated on existing plants using the data collected with the machines already present in your line to guarantee you total control and greater visibility of production processes, speed in identifying and recalling exactly the contaminated products of a given lot, and reduction of recall management costs.
Of course, traceability requirements are tailored to your company’s needs.
But it can also determine the customer’s established “acceptable” percentage of pulp and holes.
Q Eye XP uses these values as ejection criteria for crates that do not meet individual quality standards. Of course, the inspection requirements are adjusted based on product and business needs.
As an example, the maximum radiation dose absorbed by food must not exceed 10 kGy.
For example, products passing through Mito, the 3D in-line X-ray inspection device, absorb a maximum of 200 mGy per second when exposed to radiation for 1 second. Mito’s radiation dose is, therefore, 50,000 times lower than the allowable limit.
[FAQ] Frequently Asked Questions on BIOMETiC
Mito, Biometic’s in-line 3D X-ray inspection device, uses a rotating X-ray source. With a processing speed on the production line of 40m/min, in 1 second, the X-ray source makes 2 rotations around each individual object and captures about 400 internal images. These are processed in real-time and transformed into 3D reconstructions to complete evaluation of the examined product.
For example, with the 3D X-ray inspection system Mito, different containers can be scanned simultaneously, even if they are side-by-side and paired.
With Q Eye XP, an X-ray device for the end-of-line inspection of boxed fruits and vegetables and packaged food products, you can simultaneously scan multiple products within a box or package. Also, with the smart optical sorter Q Eye, you can scan multiple lines of fruits or vegetables side by side at the same time.
Images are taken along all three axes (0.5 x 0.5 x 0.5 mm) for a resolution of 1 voxel.
In fact, the detection of foreign matter in food products by Mito depends on the density difference between the foreign body and the matrix.
Contact us now to find out if we already have the application for you ready
We want to make sure we offer only the best to our customers. For the many applications tested with Mito, the false rejection rate of products with hard-to-detect foreign bodies was under 1% for the most difficult cases and under 0.1% for the most standard cases.
We also had an excellent result for the false rejection rate based on food weight measurement, considering that it is an indirect measurement: under 1%.
For example, if a food producer of toast bread produces a bread with air bubbles, and within certain size limits, he/she doesn’t consider them a defect, Mito will reject only those products with air bubbles larger than the established limits from the production line.
If, for example, a producer of jars of sauces or preserves doesn’t want to have false positives caused by air bubbles, Mito can easily detect and discard the containers containing them to exclude false positives.
For the ejection systems, you can think, for example, to install mechanical or compressed air ejectors. Contact us now and find out how easy it can be to integrate a Biometic solution within your production line.
There is no need to line up products to be scanned or position them in a particular direction to be scanned correctly by Mito. That’s because Biometic’s 3D X-ray inspection system takes advantage of all three dimensions (length, width, and depth) to scan products from all sides, so you get a three-dimensional (3D) inspection and image of the product.
Contact us now to get more details on the many benefits a Biometic solution can offer you and your company.
The scanned product thus remains unaltered because Mito acquires the data through a non-destructive analysis.
Of course, the inspection requirements are adapted according to the product and the company’s needs.
This need is growing rapidly, given the benefits of improved traceability processes. With its complete traceability system, from the goods delivered to the final product, F-Trace guarantees full traceability of your products, even those in stock.
It can be integrated on existing plants using the data collected with the machines already present in your line to guarantee you total control and greater visibility of production processes, speed in identifying and recalling exactly the contaminated products of a given lot, and reduction of recall management costs. Of course, traceability requirements are tailored to your company’s needs.
Therefore, for example, you cannot detect a foreign body in a position at an unfavorable angle to the X-ray source. To create a 3D radiographic image, however, Mito’s radiographic source rotates 360° around the food to be analyzed, thus making a cylindrical spiral movement, more or less like the computerized tomographs used in the medical field.
Together with the application of mathematical algorithms, the helical movement reconstructs a complete 3D image of the scanned product.
With Mito’s technical support, your employees can feel more comfortable in the workplace and make appropriate decisions about defective goods.
With Mito, manufacturers know the cause of the contamination and quality defect and can immediately remove only the contaminated or defective products before they reach consumers.
In a nutshell, both the manufacturer and the consumer benefit from using our inspection system.
Depending on your company’s needs, we will further adapt the software application to best manage your production process.
For this reason, we provide you with our corporate know-how and consulting services to help you choose the best Biometic solution for your needs and your company. We will support you step by step along this path:
We thought of offering you an online demonstration, during which we can find out together if you and your company can also benefit from the installation of Mito in your production.
Should Mito be suitable for your product range, we will ask you to send us samples, which we will use for initial testing.
In a subsequent appointment at our company, you will be able to see first-hand the added value you can achieve by installing our solution in your production line. Together we can also visit one of the companies where Mito is already in use.
We offer you all these services completely free of charge because we are convinced that we are the right partner for you. Contact us now to learn more!
However, with Mito, you’ll be able to measure the exact quantities in volume and weight of these ingredients. Thus you’ll avoid waste and save on resources.
For example, products passing through Mito, the 3D in-line X-ray inspection device, absorb a maximum of 200 mGy per second when exposed to radiation for 1 second. Mito’s radiation dose is, therefore, 50,000 times lower than the allowable limit.
If a food manufacturer produces special foods for specific purposes or needs to have scanning algorithms specifically developed for their products, they can be requested in individual cases.
Contact us now, and let’s evaluate together the possibilities for inspection of your products.
[FAQ] Frequently Asked Questions on BIOMETiC
Depending on the speed of the conveyor system, the average exposure time is about 1 second.
The detection rate depends mainly on the characteristics of the product to be analyzed.
Other determining factors are density, size, weight, packaging material, raw materials, etc.
We offer professional 24/7 technical support for every type of system in the appropriate language because we want to play it safe like you. In the event of technical problems, you can contact us immediately and at any time. If enabled by you, we will intervene directly on your system with remote maintenance.
We understand that every company, particularly in the food industry, is unique and has different needs. What sets us at Biometic apart is the importance we place on customization and continuous improvement of each of our solutions.
And that’s why Biometic solutions grow with your business.
Whether it’s foreign bodies or quality defects, we ensure your Biometic food inspection system always meets your needs as a producer or manufacturer, even after the sale.
Thanks in part to the use of artificial intelligence, our innovative inspection systems guarantee the best solutions for all major food and fruit and vegetable companies. In addition, our After Sales team is at your side with a range of services even after the sale:
- Spare parts packages
- Software upgrades
- Hardware upgrades
- Preventive maintenance visits on-site and remotely carried out by specialized technical staff
- On-site optimization visits with the intervention of our engineers
- Remote and on-site training sessions for your operators
Do Not Hesitate to Contact Us
We are at your complete disposal. We would be happy to provide you with our know-how and free consulting services to select the best BIOMETiC solution for your food inspection and fruit sorting needs.
Contact us now, and let’s discuss how we can make your food products and fresh produce better and more secure than ever before.